Research and Development
Our in-house research provides the foundation upon which we develop our engineering solutions, products and technology. APEX-Research B.V. is our response to the market’s growing demand for state-of-the-art services in fluid mechanics and heat transfer analysis.
In-House R&D Department
Our R&D Company APEX-Research B.V. is dedicated to broadening APEX Group’s knowledge of heat and mass transfer, fluid mechanics and the properties of potential construction materials.
To achieve this increased scope of knowledge, we employ highly educated engineers who are qualified to perform laser optical measurements and computational fluid dynamics (CFD) simulations. Furthermore, they have vast experience in the field of experimental fluid mechanics.
APEX-Research B.V.’s research activities enable us to continuously improve our products and deliver the best available engineering solutions.
"Conquer the Market Through Knowledge"
Mircea Dinulescu, Founder of APEX Group
A peek into our Laboratory
In this video, our Founder and R&D Manager present the latest innovative laser experiments. These experiments contribute to our understanding of heat exchange, and enable us to improve the sustainability of energy-intensive industrial processes.
APEX-Research offers:
- Experimental fluid dynamics (EFD);
- Flow modeling on scaled models;
- Analysis of boundary-layer phenomena;
- Heat transfer laboratory experiments; and
- Computational fluid dynamics (CFD) simulations.
Experimental Equipment:
- Laser Doppler anemometry (LDA) for accurate velocity measurements;
- Particle image velocimetry (PIV) for flow structure analysis;
- Static and dynamic pressure measurements for pressure drop analysis;
- Hot wire anemometry for turbulence analysis;
- Infrared thermometry for heat transfer analysis;
- Thermo-element measurements; and
- Latest 3D printing technology.
Advanced Laser Optical Measurement Techniques
In our lab, we use advanced laser optical measurement techniques (LDA and PIV) on transparent models. This allows us to validate our CFD analysis and to discover previously unknown behaviors in the flow of fluids.
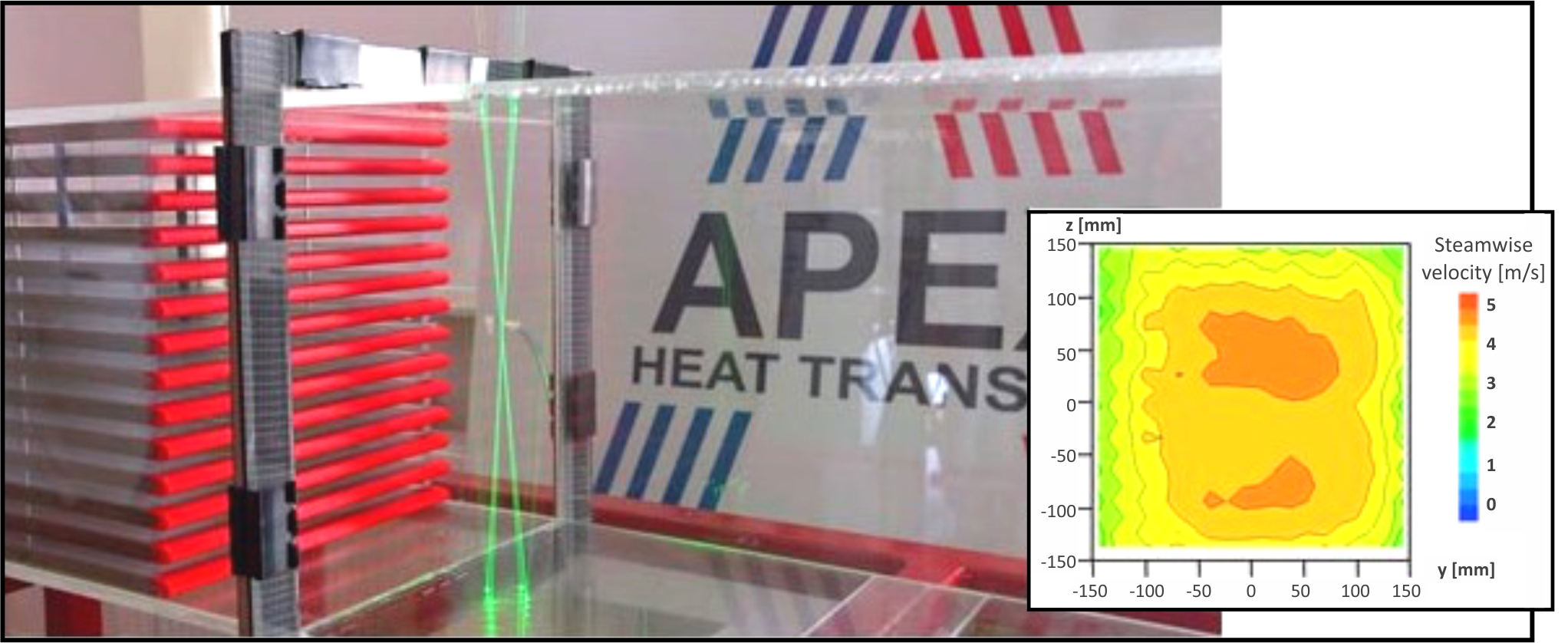
Laser Doppler Anemometry (LDA) – optical measurement technique applied to investigate flow distribution in the duct upstream the heat exchanger.
Left: Physical model of the heat exchanger (laser beams can be observed as green lines).
Right: Results of the LDA measurement taken in the cross section of the duct upstream of the heat exchanger model. Colour coding shows stream-wise velocity.
Computational Fluid Dynamics
APEX Group’s CFD simulations are able to cover complete industrial systems (e.g. a fired heater with a heat recovery system and a DeNOx SCR unit).
Our analysis is tailored to the requirements of a given case study, allowing us to find the most important improvements for the identified imperfections (e.g. flow distribution, pressure drop, mixing of the streams, vibrations, etc.).
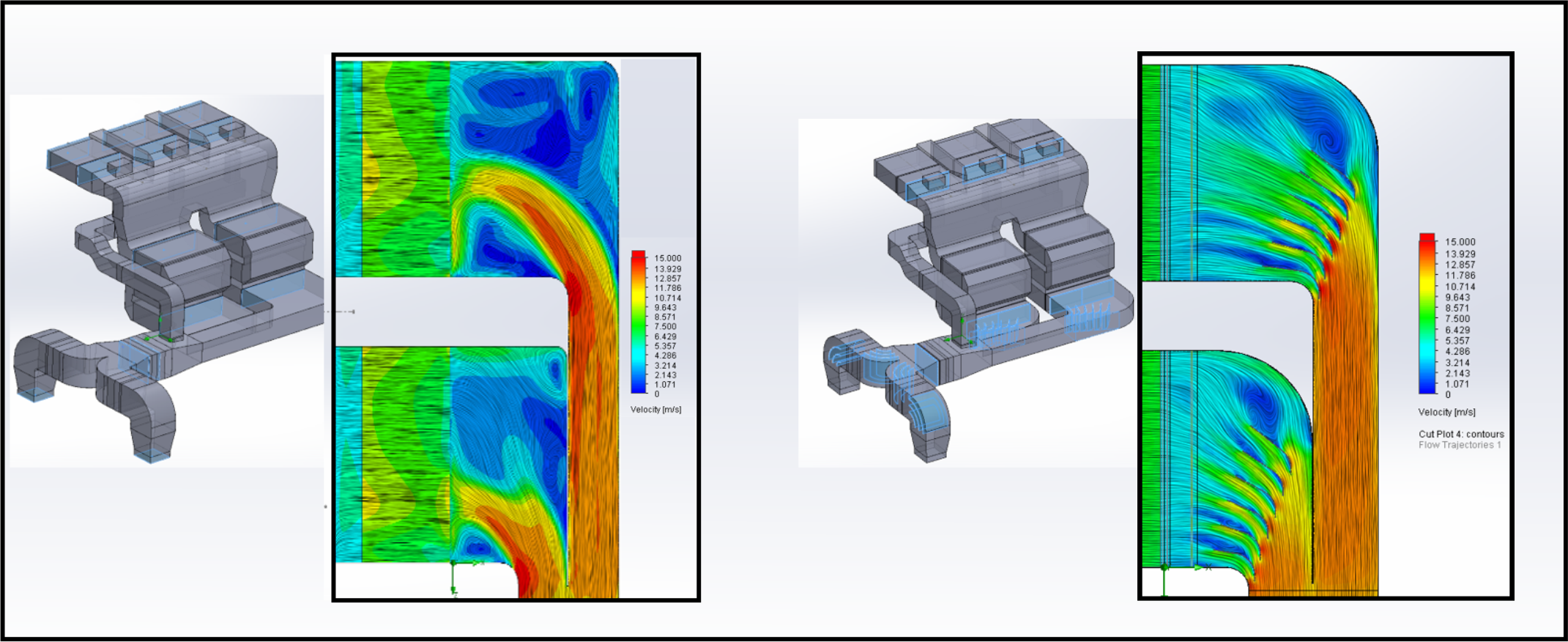
CFD simulation and optimization of the flow distribution in the duct upstream the heat exchanger. Color coding shows velocity magnitude in m/s.
Left: Original Design.
Right: Improved Design.
Case Study: CFD and EFD analysis of the flow distribution upstream the Gas-Gas Heater in the DeNOx SCR Unit
For DeNOx SCR units to perform reliably and effectively, a uniform flow velocity and temperature profile of the stream at the inlet to the catalyst are required.
If the flow distribution at the inlet to the gas-gas heater is non-uniform, then there is a major influence on the temperature distribution at the exit, upstream from the catalyst. Therefore, the flow distribution at the inlet to the heat exchanger requires special attention.
On the basis of a customer request , APEX-Research B.V. conducted a detailed investigation into the flow distribution entering the CORPEX® gas-gas heater installed in the DeNOx SCR Unit of the Waste-to-Energy plant in Barcelona, Spain. This study was aided by our state-of-the-art CFD simulations, and we validated the results using laser optical measurement techniques performed on a scaled model (i.e. LDA and PIV).
From the study we were able to identify a maldistribution of the flow at the inlet to the heat exchanger which negatively affected the performance of the catalyst. We optimized the system by adding an APEX-delfino® Flow-Conditioner, which ensured satisfactory results for the proper operation of the complete system.
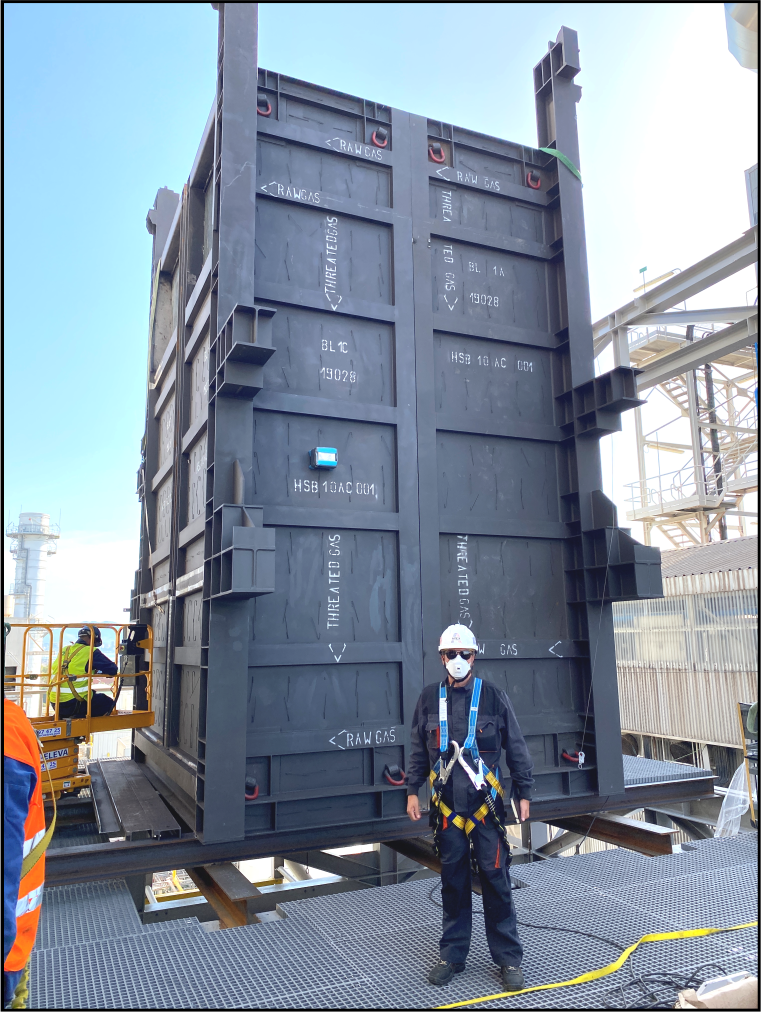
CORPEX® Gas-Gas Heater for a DeNox SCR Unit installed in a Waste-to-Energy plant in Spain.
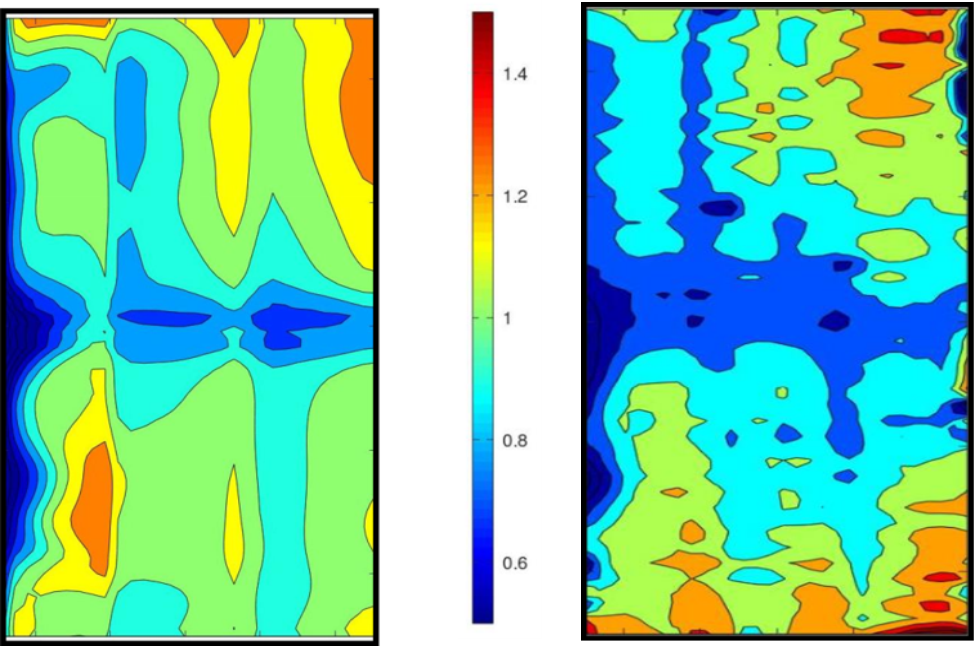
Comparison of results obtained with use of CFD simulation (left) and optical LDA measurement (right). Results show the flow distribution in the duct upstream the Gas-Gas Heater. The mean deviation from the mean velocity is 10%.
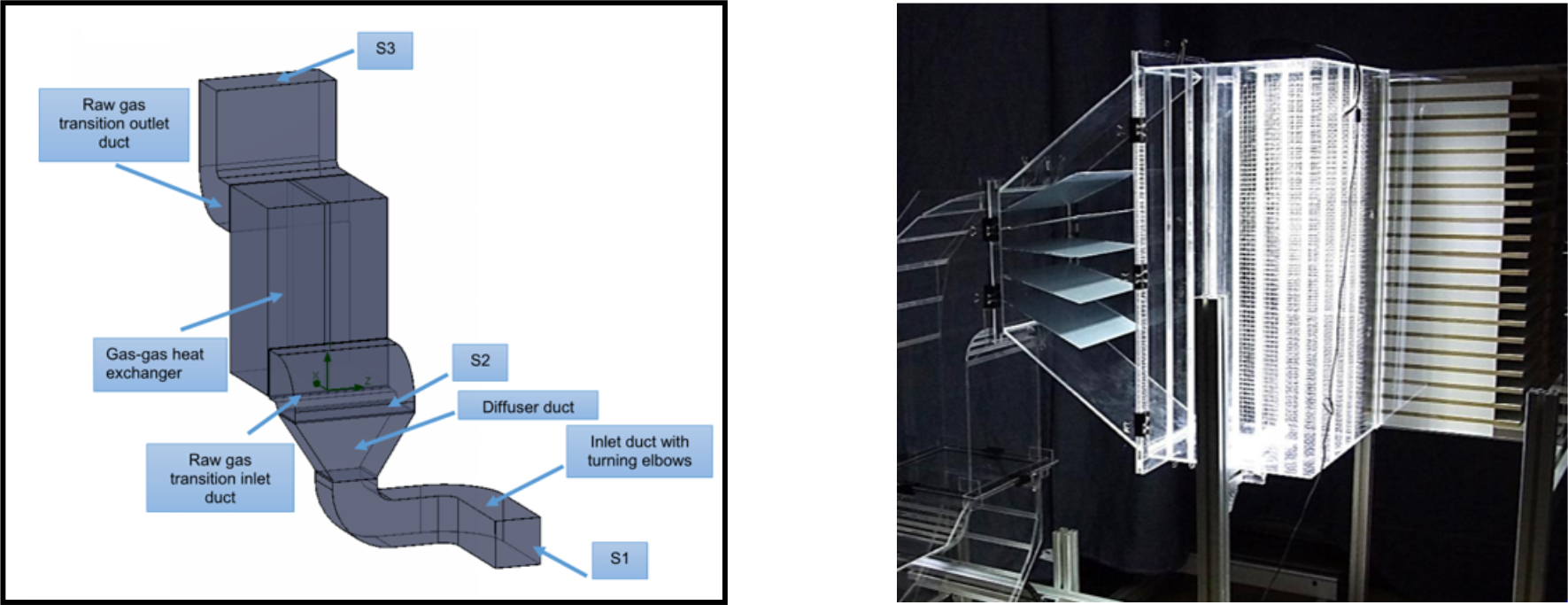
Computational model used for the CFD analysis (left) and physical model used for the optical LDA measurements (right).