APEX-delfino® Technology
“APEX-delfino® technology increases the effectiveness and lifetime of heat exchange units. This is because it offers corrosion protection, easy-access cleaning and reduced pressure drop at high heat transfer rates. APEX-delfino® technology is designed to achieve a streamlined and uniform flow, closely matching the ideal flow field characteristics without flow separation.”
– Dr. Ing. Jens Kitzhofer, R&D Manager
Optimisation and Control of the Process Stream’s Flow Field
With the use of computational fluid dynamics (CFD) simulations – validated by laser-optical measurement techniques on cold-flow models – our engineers at APEX-Research have developed the APEX-delfino® technology.
This technology provides solutions for the optimization and control of the process stream’s flow field characteristics at the inlet and/or outlet face of the heat exchanger or any other process equipment, with the lowest possible pressure drop influence on the complete process system.
Key Benefits:
- Lowered energy consumption for the pumping of fluids (i.e. forced or induced draft fan);
- Uniform outlet stream temperature for increased lifetime and/or performance of the downstream equipment (e.g. SCR catalyst, burners, bag filters);
- Uniform inlet stream velocity/temperature for increased lifetime and/or performance of the downstream equipment (e.g. air preheater); and
- Avoid fouling and corrosion of the downstream equipment (e.g. SCR catalyst, air preheater).
APEX-delfino® Technology is the foundation for the following products of APEX Group:
- Custom-design of the transition ducts
- Uniform velocity distribution at outlet
- Large static pressure recovery
- Low total pressure drop
- Match design velocity distribution
- Reduction of velocity fluctuations
- Reduced risk of corrosion
- Reduced pressure drop
- Less power consumption
- Small plot space
- Low pressure drop
- Protection of plate and edge-welds
- Easy mechanical installation
- Low pressure drop
- Large static pressure recovery
- No large-scale flow separation
- Uniform velocity distribution
- Easy mechanical installation
- Low pressure drop
- No large-scale flow separation
- Uniform velocity distribution
- Aerodynamically optimized design
- No large-scale flow separation
- Uniform velocity distribution
- Low pressure drop
- Guidance of complex flow paths
- Homogeneous static pressure distribution
- Aerodynamically optimized design
- Uniform temperature distribution
- Optimized Mixing
- Low pressure drop
- Small plot space
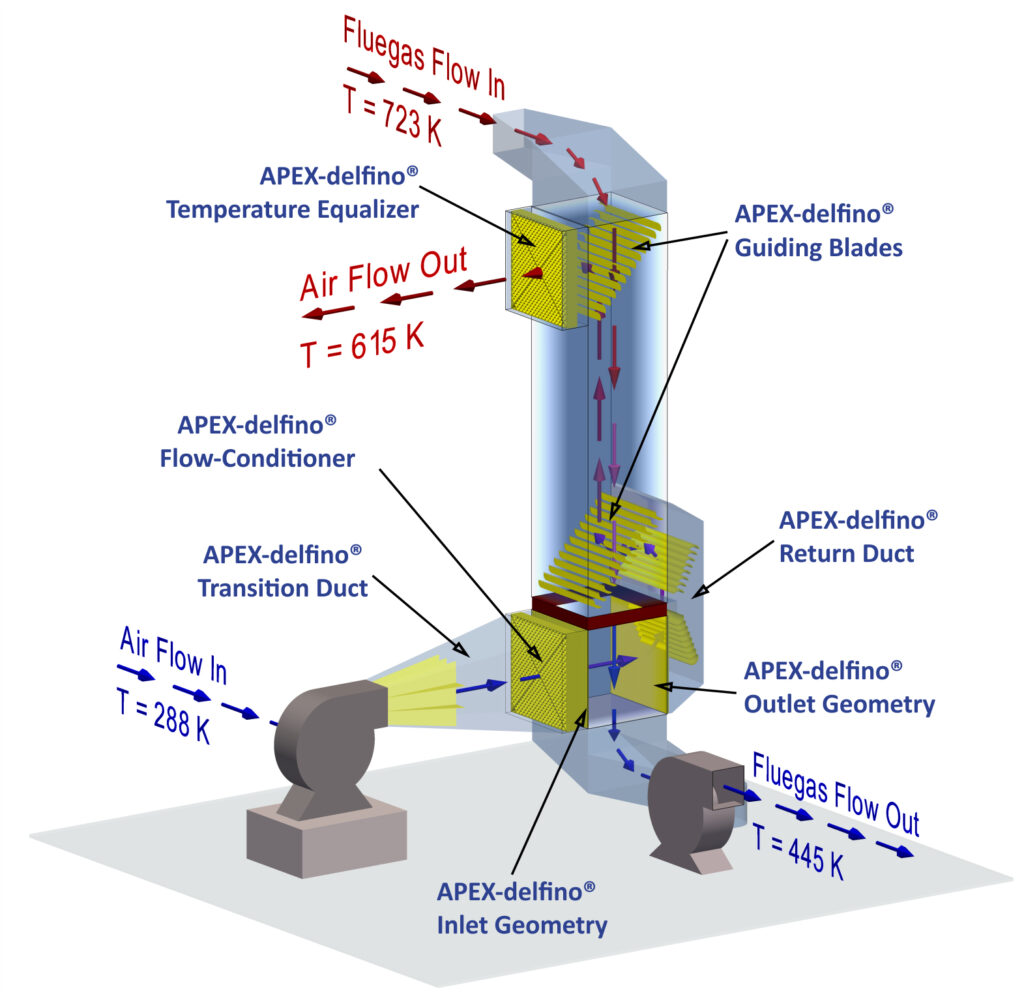
Using Computational Fluid Dynamics to Find the Best Solution:
Our CFD designs are based on extensive experimental work. By using advanced laser optical flow measurement techniques like PIV and LDA in APEX Group’s transparent flow facilities, we have gathered a deep understanding of flow fields. These techniques allow us to extract all three velocity components from a three-dimensional space. This data is used to validate our computational approach, but it also helps us to develop new innovative solutions for improving transition duct performance.
A limited plot space increases the complexity of the ducting in large heat exchanger systems. This ductwork consists of elbows changing the direction of the flow, diffusers which overcome cross sectional changes or bypasses for part-load operation.
The use of CFD identifies critical flow situations, which might influence the performance of the heat exchanger system.
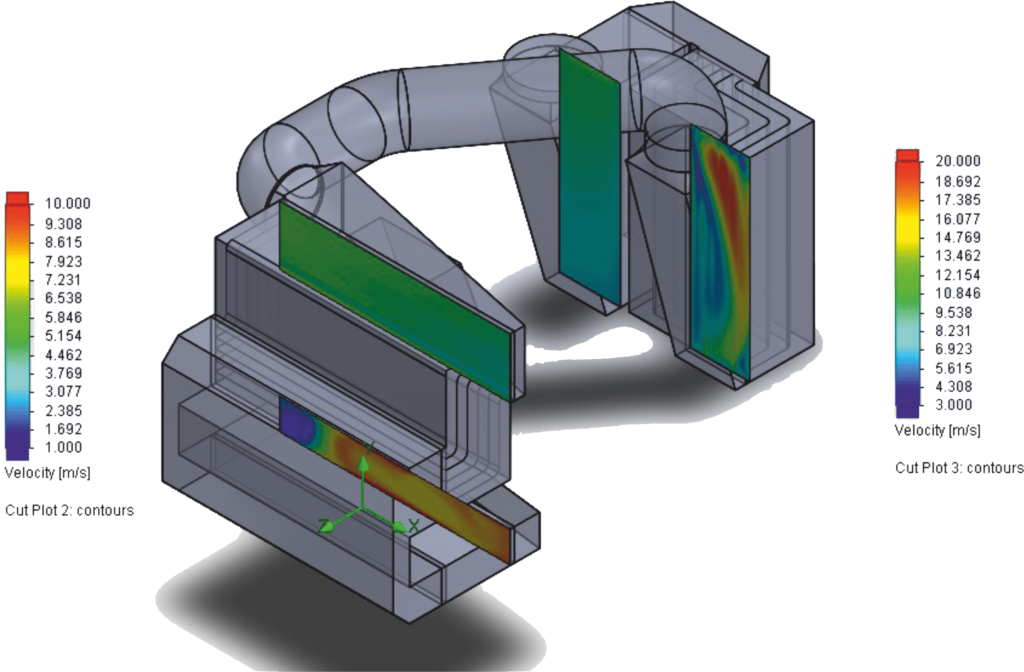
Applying flow control devices developed by APEX Group with use of CFD (and validated with use of EFD) allows the ductwork to be optimized, maximizing the flow-uniformity at the inlet into the process equipment. Additionally, our engineers seek to find an aerodynamic design with a low pressure drop and a large static pressure recovery. The combination of all these factors allows a trouble-free operation.
Services:
APEX Group can optimize the transition ducts used for feeding process equipment as well as the manufacturing of customized flow control devices. We offer this service as part of our heat exchanger design or as a stand-alone service for other process equipment which requires a uniform flow distribution.
Origin of "delfino"
The origin of the APEX-delfino® technology is twofold.
Firstly, it arises out of the long-term preoccupation of our founder Mr. Mircea Dinulescu with improving plate-type heat exchanger products. Flow uniformity in general has been of particular interest, with Mr. Dinulescu striving to eliminate flow separation and dead-water regions.
Secondly, the technology is inspired by nature. In his observations of playing dolphins, Mr. Dinulescu noticed how they caused virtually no disturbance to the water. Therefore, he was inspired to create a heat-transfer geometry mimicking their interconnection with water.
And thus:
- the dolphin’s nose became APEX-delfino® Inlet Geometry;
- the dolphin’s fins became APEX-delfino® Guiding Blades;
- the dolphin’s tail became APEX-delfino® Outlet Geometry;
- the dolphin’s streamlined body became APEX-delfino® Transition Duct; and
- the APEX-delfino® Flow-Conditioner and the APEX-delfino® Temperature Equalizer, exterior to the dolphin’s body, followed as logical extensions.
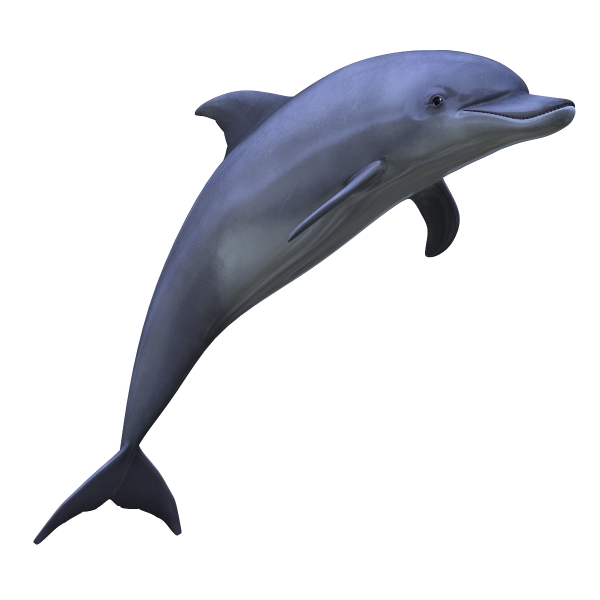