V-FLEX® Vortical Flow Heat Exchangers
Based on its expertise in designing and manufacturing high-quality, heavy-duty heat exchangers, APEX Group developed the patented V-FLEX® product line. V-FLEX® products combine the advantages of both plate-type and tubular heat exchangers.
V-FLEX®: The best of both worlds
The efficiency of a plate-type heat exchanger
Plate-type heat exchangers have several advantages over their conventional tubular counterparts. They are more compact, have a lower operating pressure drop, have a lower fouling tendency and have a higher thermal efficiency. This leads to lower operating costs since energy consumption and maintenance costs are decreased. Furthermore, it guarantees a smaller environmental footprint as CO2 emissions are reduced.
Since V-FLEX® heat exchangers use elongated heat transfer elements rather than round tubes to construct their flat or undulated heat transfer panels, it ensures that they have all the advantages associated with plate-type heat exchangers.
The pressure resistance of a tubular heat exchanger
Despite the many advantages of plate-type heat exchangers, they have one key limitation: their typical differential pressure limit is 0.5 barg. Therefore, under some operational conditions, tubular heat exchangers may be preferred.
The appeal of the V-FLEX® product line is that it combines the benefits of traditional plate-type and tubular heat exchangers. Not only are V-FLEX® products able to reduce operating costs and CO2 emissions, they can also support pressures from 0.5 barg up to 5 barg (irrespective of whether the fluids are gaseous, liquid, or multi-phase).
Key Features
Characteristics:
- Constructed from elongated rectangular elements
- Offers advantages of both the plate type and the tubular heat exchanger:
- high thermal efficiency
- increased differential pressure resistance
- The working fluid inside the heat transfer element can be gaseous, liquid or multi-phase
- Higher resistance to cyclic temperature loads
- Modified geometry of the heat transfer surface to enhance the heat transfer coefficient with VORTI-FLEX® Technology
- Suitable for working with corrosive (condensing) fluids (with A-CORREX® Technology)
Fluids Handled:
- Combustion air
- Flue gas from combustion of: gaseous fuels, liquid fuels, solid fuels, waste, biomass
- Vapor (condensing or non-condensing)
- Industrial exhaust streams
- Liquids (i.e. water, steam)
Typical Services:
- Combustion Air Preheater
- Gas-Gas Heater
- Flue Gas Cooler/ Condenser
- Gas Turbine Exhaust Gas Cooler
Typical Technical Specifications:
- Heat Transfer Plate Thickness: 1.2 to 4 mm
- Design Temperature:
- Up to 900 °C for metallic
- 200 °C for polymer composite
- Design Differential Pressure:
- up to 5 barg for metallic
- 0.1 barg for polymer composite
- Duty Range: Unlimited
- Thermal Effectiveness: ~97%
- Pressure Drop Rates: 0 to 0.1 bar
- Leakage Rates: 0 to 0.5%

A-CORREX® Technology
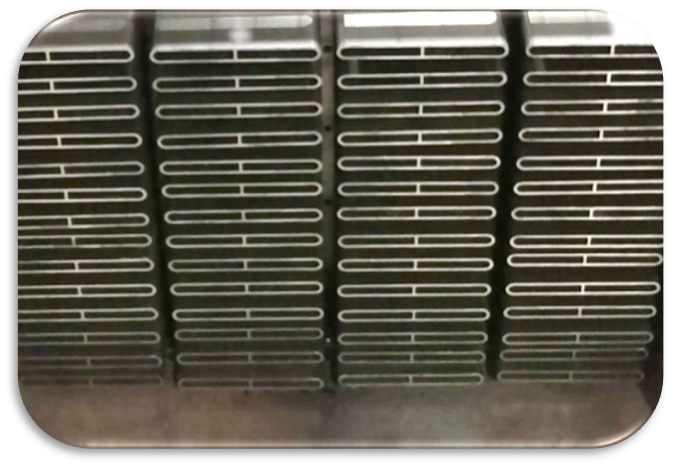
Applicable Technologies:
- APEX® Free-flow Technology – minimizes the flow separation & fouling tendency; this makes the product easier to clean.
- AIR CURTAIN® Technology – controls the heat transfer surface temperature to avoid “cold corner” corrosion.
- APEX® VariaFlow – ensures a uniform flow-field temperature profile at the fluid outlet.
- APEX® Erosion Technology – improves the heat transfer elements’ ability to withstand erosion.
- A-CORREX® Technology – prevents acid dew point and water dew point corrosion.
- APEX-delfino® Technology – optimizes the fluid flow distribution and temperature profile.
- VORTI-FLEX® Technology – enhances the heat transfer coefficient between two fluids in laminar or transient flow.
Extra Benefits
Easy maintenance with APEX® Free-flow Technology
APEX® Free-flow Technology is included in all V-FLEX® heat exchangers. This technology reduces operational costs by lowering the maintenance requirements of the heat exchanger. Firstly, it prevents the formation of large and undesired flow recirculation zones inside the heat transfer core, minimizing the risk of fouling and erosion. Secondly, it ensures that the heat transfer surfaces are easily accessible for cleaning.
Can be operated in corrosive environments
By applying A-CORREX® Technology to V-FLEX products, the heat exchangers can be safely operated in corrosive environments. This opens new possibilities for their use in emerging technologies, such as in carbon capture and storage (CCS), which require fluid gas temperatures to fall below the acid dew point.
VORTI-FLEX® Technology
By applying the VORTI-FLEX® Technology the shape of the inner and outer surfaces of the V-FLEX®’s heat transfer elements can be manipulated with minimum effort, enabling the turbulence of the fluid flow field to be increased for maximum efficiency at the lower Reynold’s numbers.